How to Use Manufacturing Quality Engineering to Reduce Defects and Improve Efficiency
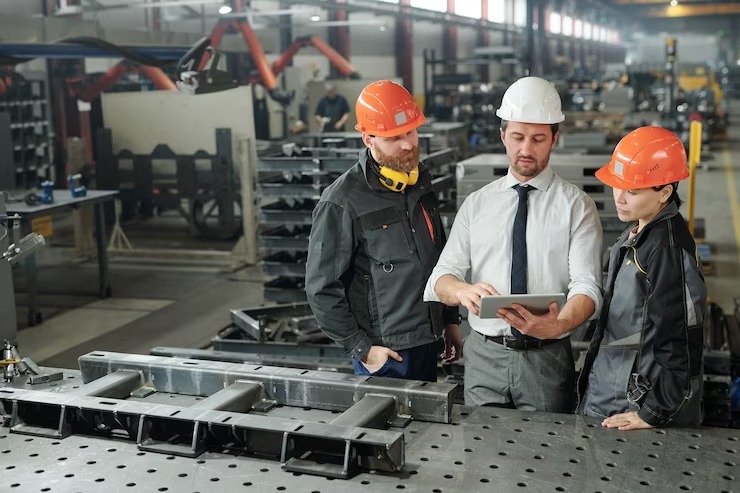
In manufacturing, achieving perfection is an ongoing journey filled with challenges. The battle against defects and the pursuit of enhanced efficiency is unending. However, Manufacturing Quality Engineering serves as a guiding light in this journey. In this comprehensive guide, we will delve into the intricacies of Manufacturing Quality Engineering, exploring how it can be harnessed to minimize defects and boost operational efficiency. We will introduce you to AmrepInspect, a reputable quality control and inspection services provider, to help answer your questions and provide practical solutions.
1. Understanding Manufacturing Quality Engineering
What is Manufacturing Quality Engineering?
Manufacturing Quality Engineering is a systematic approach to ensure that products meet predefined quality standards throughout production. It involves the application of engineering principles, statistical analysis, and continuous improvement methodologies to maintain and enhance product quality.
Quality engineers are vital in designing, implementing, and monitoring processes to minimize defects, reduce variations, and optimize efficiency. They collaborate closely with production teams, using data-driven insights to pinpoint areas for improvement and implement changes that lead to higher-quality products.
The Significance of Quality Engineering
Quality engineering is the backbone of any successful manufacturing operation. It underpins consumer trust in products, influences brand reputation, and, most importantly, can save a business from costly recalls and reputation damage. By proactively addressing quality issues at every production stage, quality engineering helps prevent defects, ensuring products meet or exceed customer expectations.
Quality engineering is also a strategic investment. It can reduce production costs, minimize waste, and improve efficiency. Consequently, businesses can allocate resources more effectively and remain competitive.
2. Why Manufacturing Quality Engineering Matters
Reducing Defects in Manufacturing
Defects in manufacturing can be costly and detrimental to a brand’s reputation. Manufacturing Quality Engineering is instrumental in the early detection and prevention of defects, reducing the likelihood of defective products reaching customers.
Root Cause Analysis: Quality engineers employ analytical tools to identify the root causes of defects. Addressing these causes prevents defects from recurring.
Improved Process Control: Quality engineering ensures that production processes are stable and within acceptable limits, reducing the chances of defects occurring due to process variations.
Product Testing and Inspection: Robust quality engineering practices encompass systematic product testing and inspection at various stages of production to catch defects before they escalate.
Boosting Operational Efficiency
Efficiency is a critical metric in manufacturing. Quality engineering plays a pivotal role in achieving and maintaining it.
Reduced Rework: By minimizing defects, quality engineering reduces the need for rework or production restarts, which can consume significant resources.
Optimized Resources: Quality engineering helps identify areas where resources can be optimized. This includes labor, materials, and equipment.
Streamlined Processes: Quality engineering often leads to the streamlining of processes, resulting in shorter lead times and faster product delivery.
3. Key Principles of Manufacturing Quality Engineering
Manufacturing Quality Engineering is founded on fundamental principles that guide its implementation and success. Let’s explore these principles in detail.
Data-Driven Decision-Making
Gathering and Analyzing Data: Quality engineers collect data from various sources, such as production processes and quality control tests. This data is analyzed to identify trends, correlations, and areas of improvement.
Statistical Analysis: Statistical tools and techniques, like Six Sigma, are used to make informed decisions based on data analysis. These tools help in predicting and preventing defects.
Fact-Based Problem Solving: Data-driven decision-making ensures that problems are addressed based on facts and evidence rather than assumptions. This leads to more effective solutions.
Continuous Improvement
Kaizen Philosophy: The philosophy of continuous improvement is central to quality engineering. It involves ongoing efforts to enhance processes, products, or services incrementally.
PDCA Cycle: The Plan-Do-Check-Act (PDCA) cycle is a common approach for continuous improvement. It involves planning changes, implementing them, checking the results, and acting on the findings to make further improvements.
Learning Organization: Quality engineering encourages organizations to become learning organizations where lessons from each improvement cycle are applied to the next.
Process Optimization
Process Mapping: Quality engineers map out production processes to identify bottlenecks, inefficiencies, and areas where improvements can be made.
Lean Principles: Lean manufacturing principles are often applied to optimize processes by reducing waste, minimizing inventory, and improving overall workflow.
Automation and Technology: Integrating automation and advanced technologies is another aspect of process optimization, helping to improve efficiency and reduce human error.
4. Tools and Technologies in Manufacturing Quality Engineering
AmrepInspect: Your Partner in Quality Control
Regarding quality control and inspection services, AmrepInspect is a reliable and experienced partner for businesses seeking to enhance their manufacturing quality engineering practices.
Expert Inspection Services
AmrepInspect offers various inspection services, including pre-production, in-process, and final inspections. These inspections help identify defects and ensure that products meet established quality standards.
Quality Control Consulting
AmrepInspect’s experts provide quality control consulting, offering guidance on improving production processes and reducing defects. Their experience spans various industries, making them a valuable resource for businesses.
Reporting and Analytics
AmrepInspect provides detailed reports and analytics that offer insights into the quality of products and production processes. This data can be used to make informed decisions and drive improvements.
Statistical Process Control (SPC)
Process Monitoring: SPC involves monitoring key process parameters to ensure they remain within defined control limits. Any deviation from these limits can indicate a potential issue.
Variation Analysis: SPC uses statistical analysis to study process variation and identify its sources.
Control Charts: Control charts are a standard tool in SPC, providing a visual representation of process data and enabling the early detection of anomalies.
Failure Mode and Effects Analysis (FMEA)
Identifying Failure Modes: FMEA involves identifying all possible failure modes for a product or process and assessing their potential effects.
Severity, Occurrence, and Detection: FMEA assigns a rating to each failure mode based on severity, occurrence, and detection. This helps prioritize which issues to address first.
Risk Mitigation: By identifying high-risk failure modes, FMEA enables the development of strategies to mitigate these risks and prevent defects.
In the dynamic manufacturing world, embracing Manufacturing Quality Engineering is the path to reduced defects and improved operational efficiency. Businesses can meet or exceed customer expectations by leveraging data-driven decision-making, continuous improvement, and process optimization while maximizing operational efficiency. With AmrepInspect as your trusted partner, you can take these principles into action and secure a competitive edge in the market.