How Box Build Assembly Enhances Your PCB Assembly Process
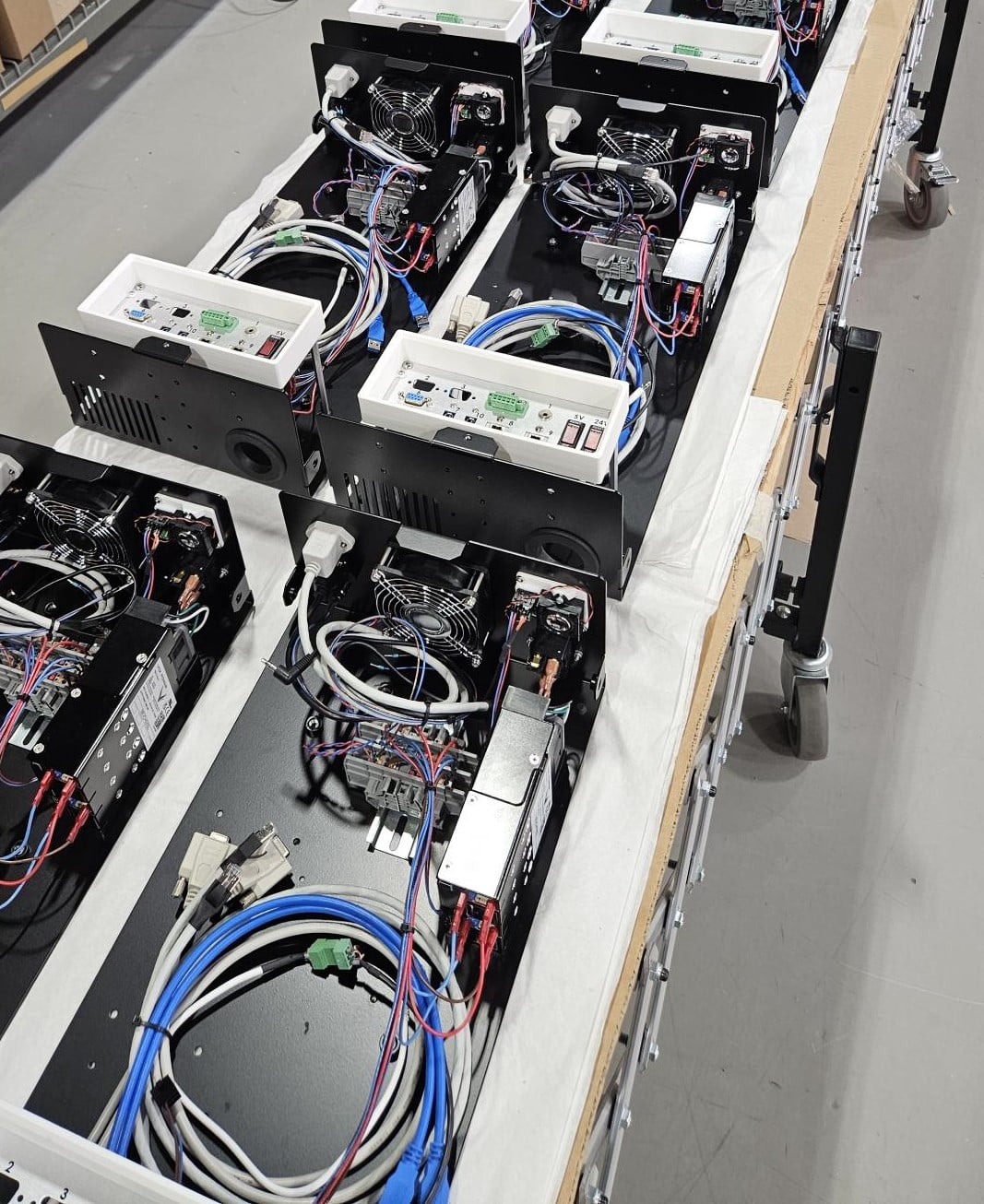
Table of Contents
ToggleIn the realm of electronics manufacturing, PCB assembly and box build assembly are two integral components of the production process. While PCB assembly focuses on creating the core electronic circuits that power a device, box build assembly plays a crucial role in bringing these components together into a complete, market-ready product. In this article, we’ll explore how box build assembly enhances and complements the PCB assembly process, ensuring that the final product is functional, reliable, and ready for use.
Understanding the Basics of PCB Assembly
PCB (Printed Circuit Board) assembly is the process of attaching electronic components, such as resistors, capacitors, transistors, and integrated circuits, to a PCB. These boards are the foundation of any electronic device, acting as the “brain” of the system by providing a platform for electrical connections.
There are two main methods used in PCB assembly:
-
Surface Mount Technology (SMT): Components are mounted directly onto the surface of the PCB.
-
Through-Hole Technology (THT): Components are inserted into holes drilled into the PCB and soldered in place.
Once the components are attached, the PCB undergoes various tests to ensure proper functionality, such as in-circuit testing (ICT) and automated optical inspection (AOI).
What is Box Build Assembly?
Box build assembly is the process of integrating various components into a final product enclosure or “box.” After the PCB assembly services process, the PCB needs to be integrated with other elements such as wiring, connectors, power supplies, mechanical components, and enclosures to form a fully functional product.
Box build assembly can encompass several tasks, including:
-
Component integration: Including mounting the PCB inside a protective enclosure, connecting the PCB to external connectors, and installing wiring.
-
System assembly: Assembling other subassemblies like sensors, displays, power modules, and more.
-
Software installation: Loading firmware or software necessary for the device to function.
-
Final testing: Ensuring the entire system functions correctly and meets regulatory standards.
While the PCB assembly ensures the electronic components are ready for operation, box build assembly ensures that the product is ready to function in a real-world environment.
How Box Build Assembly Enhances PCB Assembly
The synergy between box build assembly and PCB assembly is essential for creating high-quality, fully functional products. Here’s how box build assembly enhances the PCB assembly process:
1. Creating a Complete Product
After the PCB assembly is completed, it’s time to integrate the PCB into the final product. This is where box build assembly truly shines. Box build assembly takes the individual, assembled PCB and integrates it with other key components to create a complete, working system.
This integration can involve:
-
Mounting the PCB: The assembled PCB is typically housed inside an enclosure, which may be custom-designed for the product. This enclosure is not just for protection; it may also include mounting points for the PCB and ensure that the device can withstand mechanical stress.
-
Connecting additional components: In most electronic products, the PCB must be connected to other components, such as power supplies, displays, buttons, and connectors. Box build assembly facilitates this integration, ensuring all components are properly connected.
Without box build assembly, the assembled PCB would remain a standalone component, unable to function as part of a larger system.
2. Improving Product Reliability and Durability
One of the main functions of box build assembly is to provide the necessary protection for the PCB and other sensitive components. The enclosure ensures that the electronics are shielded from dust, moisture, physical damage, and electromagnetic interference.
Box build assembly also involves:
-
Mechanical design considerations: The enclosure is designed to protect the PCB and prevent it from being exposed to external environmental factors that could harm its performance.
-
Thermal management: In certain products, heat management is critical. Box build assembly may include the installation of cooling solutions such as fans, heat sinks, or thermal pads to ensure that the PCB and other components don’t overheat.
By addressing these concerns, box build assembly significantly enhances the longevity and reliability of the product, ensuring that it can function properly under real-world conditions.
3. Streamlining the Manufacturing Process
Box build assembly and PCB assembly often complement each other to streamline the overall manufacturing process. When both processes are handled by the same company or team, communication is simplified, and the integration of components becomes more seamless.
By consolidating both services under one roof, manufacturers can:
-
Minimize lead times: The box build assembly team is already familiar with the specifications of the PCB, allowing for faster integration and assembly.
-
Ensure consistent quality: The same company handling both PCB and box build assembly can implement consistent quality control measures across both processes.
-
Reduce errors: With both the PCB assembly and box build assembly managed by the same team, the likelihood of mistakes or miscommunications is reduced, leading to fewer defects and delays.
This streamlined approach helps to reduce costs and improve overall efficiency, allowing companies to bring their products to market faster.
4. Customization and Flexibility
Box build assembly provides an opportunity for customization that enhances the PCB assembly process. In many cases, the PCB may be designed with specific functional requirements in mind, but the box build assembly allows for flexibility in how these components are housed and integrated.
For example:
-
Custom enclosures: Depending on the application, the enclosure for the product may need to be tailored to meet certain size, aesthetic, or durability requirements. This customization ensures that the final product fits the design specifications and performs optimally.
-
Additional functionality: Box build assembly can involve adding features like touchscreens, buttons, LEDs, or additional sensors, enhancing the functionality of the assembled PCB and expanding the product’s capabilities.
By working closely with both the PCB and box build assembly teams, manufacturers can create products that meet specific design and performance requirements.
5. Final Testing and Quality Assurance
Once the PCB and box build assembly are complete, the product undergoes final testing to ensure that everything works as expected. This includes functional testing, safety checks, and compliance with industry standards.
Box build assembly plays a crucial role in ensuring that all components are properly integrated and function together as a complete system. Some of the key testing procedures include:
-
In-circuit testing (ICT): This checks the PCB for short circuits, open circuits, and other electrical faults.
-
System-level testing: This involves testing the entire assembled product to ensure that all parts are functioning as they should.
-
Environmental testing: For products that will be used in harsh conditions (e.g., automotive or outdoor applications), box build assembly can include tests to simulate real-world environments, such as temperature fluctuations or humidity exposure.
Final testing ensures that the product meets performance standards and is free from defects before it reaches the customer.
Conclusion
Box build assembly is an essential process that enhances and complements the PCB assembly process. By integrating the PCB with other key components, providing protection, improving durability, and ensuring functionality, box build assembly plays a vital role in creating a high-quality, market-ready product.
Together, PCB assembly and box build assembly form the foundation of modern electronic manufacturing, ensuring that products meet the rigorous demands of today’s consumers and industries. By understanding the synergy between these two processes, manufacturers can deliver products that are not only reliable and functional but also ready to perform in real-world condition.